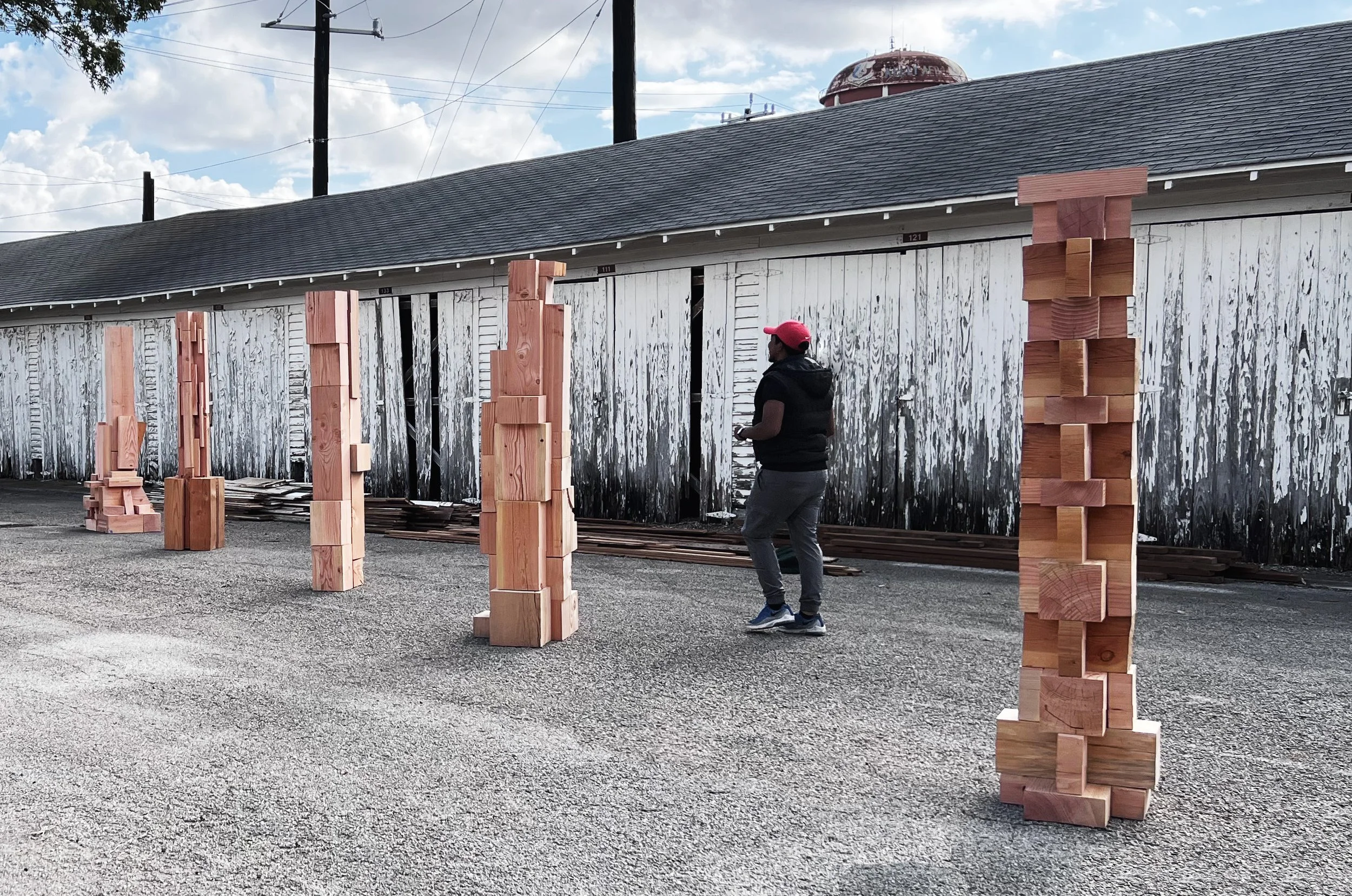
Carbon Sequestration
in Lumber Columns
Facilitating the reuse of lumber waste for prefabrication through computational design and augmented fabrication
Resource-Efficient Prefabrication.
Introducing a revolutionary solution for resource-efficient prefabrication - the research project presents a construction framework that enables the reuse and salvaging of lumber waste from a lumber construction company. The cutting-edge approach employs Computational Design and Augmented Reality (AR) technology to develop a new process for utilizing scrap materials.
AR Application
Unlike traditional methods that promote downgrading, the framework utilizes an inventory of scrap materials to design columns and proposes a high level of automation (LoA) prefabrication for reusing lumber waste for structural parts. The design and AR framework feature a design tool for placing existing lumber scrap blocks and an integrated AR application for assembling these blocks into wood columns, extending the opportunities for designers to reuse lumber scraps for prefabrication. The project simplifies assembly instructions for craftspeople and creates valuable tools for enabling a resource-efficient workflow for lumber scrap. The setup is demonstrated through column prototypes, resulting in six columns, each 10 feet high, that showcase the potential of the proposed methods.

“It all begins with an idea. Maybe you want to launch a business. Maybe you want to turn a hobby into something more. Or maybe you have a creative project to share with the world. Whatever it is, the way you tell your story online can make all the difference.”
— Squarespace
AR Framework
We have developed an innovative solution for overcoming the challenges of matching non-standard blocks with assembly tasks. Our team programmed an augmented reality (AR) tool using Fologram and Grasshopper, which can be used on both mobile devices and the Microsoft HoloLens 2.
Participants can easily access the app using up to three smartphones connected to a private Wi-Fi network, which allows for seamless data transfer to and from the design environment. The AR tool we developed is incredibly versatile, displaying all possible assembly stages through a colour gradient indicator.
AR Headset
Our tool projects a full-scale 3D model, which can be positioned manually or via a QR marker. Users can also adjust the range of displayed blocks using two handy sliders, one for the lower and one for the upper bound.
With this AR tool, designers can easily visualize and assemble non-standard blocks, making the design process more efficient and effective. Our tool is an excellent example of how technology can be used to enhance design and make it more accessible to everyone.

Material Donations by
Timberlyne
Captured Scrap Material
If you're looking to incorporate reclaimed lumber blocks into your design project, the process can vary depending on your specific needs and goals. One of the first steps is to identify where to source the material. Potential suppliers might include salvage yards, wood reclaimers, or deconstruction contractors.
In a recent case study, we obtained our reclaimed lumber blocks from a lumber construction company specializing in medium to large-scale post and beam constructions. We were provided with cut-off pieces from solid lumber, mainly consisting of green Douglas fir, Cider, Pine, and Oak. The blocks varied in size, with some smaller triangles measuring around 20 cm on each edge, and larger blocks measuring approximately 40 x 40 x 100 cm.
To collect the blocks, we arranged for pickup at the end of each week using a pickup truck, and stored them at a nearby wood shop. With the right sourcing and storage strategies, incorporating reclaimed lumber blocks into a design project can be a rewarding and sustainable choice.
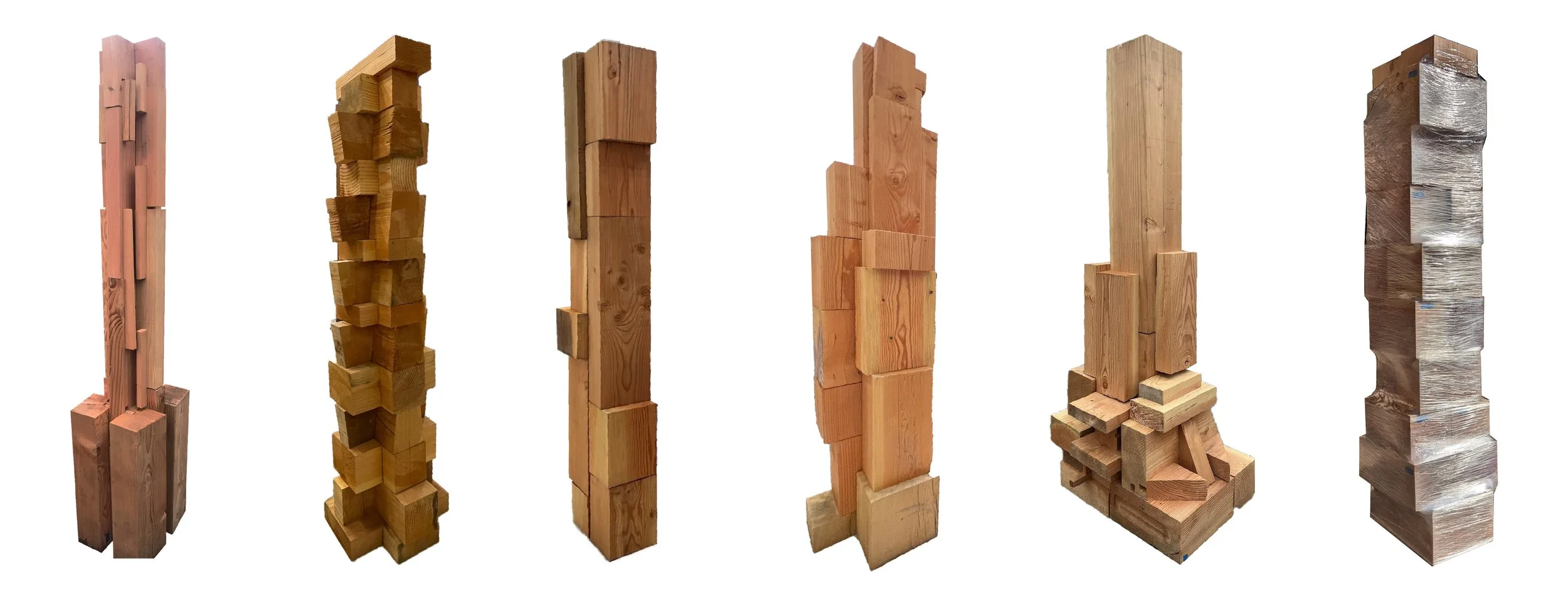
C02 Storage
Our research has provided valuable insights into working with non-standard lumber parts and utilizing waste products from prefab factories and deconstructions. By offering practical tools and knowledge, we have created an approach that promotes the reuse of building materials, while also reducing waste and maximizing efficiency.
Our design iterations showcased a spectrum of approaches and a shift towards building components as carbon sinks. Initially, our focus was on elaborate connection details for dry-joined interlocking of the blocks. However, this method created too much waste due to the many necessary cuts. As a result, we shifted our focus to minimize and avoid all cuts in later prototypes.
While building a column might seem like a small contribution to an architectural structure, our work has shown that by reducing cutting, we can almost double the CO2 storage in a single column. Our proposed designs challenge the dominant notion in computational design of material efficiency and instead emphasize the storage of CO2 within building elements.
The saved CO2 emissions from our approach are equivalent to emissions from heating a home for a year with natural gas, burning approximately 220 gallons of gasoline, or manufacturing approximately 700 pounds of cement. By prioritizing CO2 storage and minimizing waste, we can make a significant impact on reducing our carbon footprint and building a more sustainable future.
Project Team
Material Donations:
Alex Arunda and Eric J. Arnold from Timberlyne
Wood Shop Coordinator:
Patrick Page Sutter
UTSA Large Scale Testing Lab:
Prof. Wassim Ghannoum, PhD
Instructor:
Prof. Dr. Bastian Wibranek
Students of the Digital Design and Fabrication class of the Fall Semester 2023:
Aguilar, Gerardo A. Al Saadi, Evan Alvarado, Victor Bernal Jara, Andrea E. Forney, Joshua I. Leiva, Elsa K. Maldonado Hernandez, Nixon I. Medellin, Elizabet Milbes, Ayah B. Ortiz, Claudia C. Padilla, Yaire O. Perea, Fabian R. Sanchez, Ana I. Shaheer, Jameel Thompson, Kyndal M. Zuniga, Mauro A.